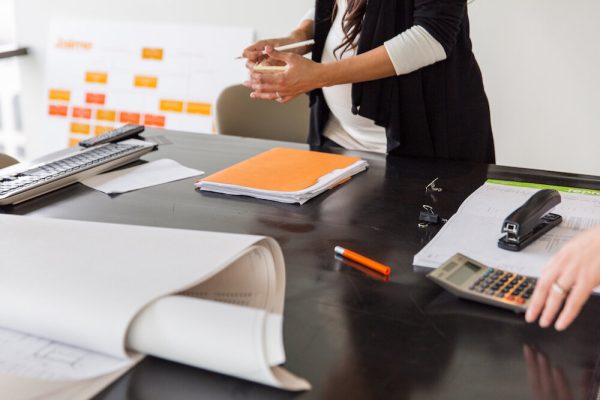
The turnover phase of a construction project is the systematic transition of building operations from the project team to the operation and maintenance (O&M) team. The transition is the physical completion of the construction project and includes the transfer of knowledge in the form of documentation. A successful transition is one where documentation is complete, well-organized and, most importantly, buildings systems operate per design and O&M personnel are trained to operate the systems.
Updated As-Built Documentation
Construction projects are guided by design documents that explain and detail the thousands of working parts that need to come together for a successful turnover. During construction, design documents undergo revisions due to site conditions or unforeseen issues. Drawings are red lined in the field by contractors installing equipment, detailing specific equipment installation, physical locations as well as other updates.
The construction manager needs to be aware of changes as they affect equipment and receive updated documentation from the project team. While the construction manager is not responsible for updating design documents, he/she is responsible for making sure red lined updates are reflected in as-built drawings provided to the owner – specifically, mechanical and controls as-builts. As-builts will provide the O&M personnel with exacting information with which they can locate equipment, troubleshoot system issues, trend equipment performance and transfer knowledge to new personnel as needed.

Provide a Systems Manual
The systems manual is not always required as part of the turnover package – unless the project is pursuing LEED certification. However, it is an invaluable resource that can ensure a successful turnover. The systems manual is a comprehensive guide that should describe systems, control sequences and best practices for maintaining equipment. Further, a systems manual should include control drawings, riser diagrams, and control sequence highlights. A systems manual is a tool that can be used by O&M personnel to operate, troubleshoot, maintain and track building performance.
Lessons Learned Session
The final capstone to every successful project is a “lessons learned” meeting with the building owner, O&M personnel and select project team members. Lessons learned can be used to help inform the owners understanding of what worked and what didn’t work.
The best practices mentioned here can help ensure the owner and O&M personnel are well informed of building systems, have the necessary documentation to operate and maintain the building, as well as an understanding of the lessons learned during the construction project.
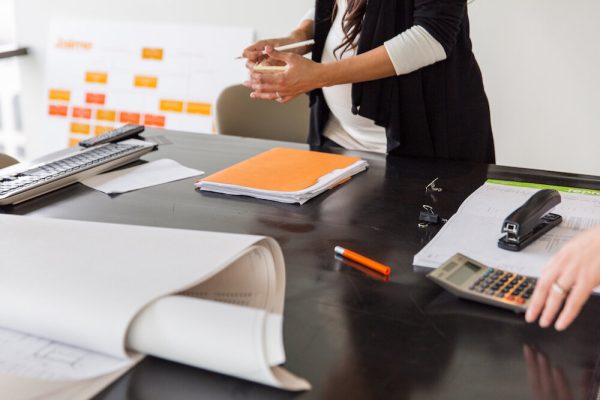